With the RX 4.0 thermoformer packaging machine that meets GMP standards, MULTIVAC is establishing new benchmarks in the medical and pharmaceutical sectors. A Yaskawa six-axis robot, compliant with GMP standards, is utilized at the end of the line for the first time. This offers numerous benefits, especially a significant advantage in flexibility.
The MULTIVAC Group, located in Wolfertschwenden, Germany, has established a reputation for tailored packaging solutions in the pharmaceutical, medical, and food sectors. The company’s portfolio, established in 1961 and employing approximately 7,400 individuals, comprises a range of packaging technologies, automation solutions, labeling and inspection systems, and, importantly, packaging materials.
The rising need for precision and consistency in the medical and pharmaceutical sectors concerning the packaging of delicate products led MULTIVAC to create a thermoforming packaging machine that aligns with the heightened standards of clients, the marketplace, and regulations. Simultaneously, the RX 4.0 machine has achieved a reduction in throughput times while enhancing production efficiency and flexibility.
Debut: Implementation of a GMP-compliant six-axis robot
A novel aspect of the packaging machine is the incorporation of a six-axis robot designed for the medical and pharmaceutical industries, marking the first instance of MULTIVAC utilizing an external product. Creating our own six-axis kinematics would not have been logical given our current product lineup. “That is the reason we chose a robot from Yaskawa,” states Wolfgang Buchenberg, Senior Director of Technical Solutions at MULTIVAC.
An examination of the machine’s operation clarifies why the packaging expert preferred six-axis kinematics for the new device. In the initial step, a SCARA robot, developed in-house by MULTIVAC, places the items to be packaged into the thermoformed cavities created by the thermoformer packaging machine. The RX 4.0 manages the other main packaging tasks, such as sealing the bottom film with a top film that is printed inline in various colors prior to sealing. Next, a visual check of the print image occurs, followed by separating the packs through a complete cut.
Six axes for even more flexibility
At the output of the thermoformer packaging machine, the packs are removed directly from the cutting unit and separated by the Yaskawa robot. Wolfgang Buchenberg explains why the use of a six-axis robot is the best choice here: “Using the MOTOMAN HD7 has decisive advantages, especially in terms of flexibility. We can unload using single or multiple picks. In our demo system, for example, we use a five-pick vacuum gripper. Packs can also be separated on moving conveyors or at defined stationary positions. And thanks to the six axes, we have no limitations in terms of access to positions and can handle many different formats.
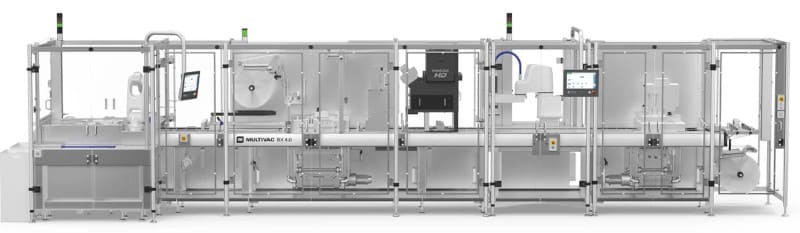
MULTIVAC’s decision to use Yaskawa six-axis robots in its thermoforming packaging machines was not an easy one. On the contrary: In a detailed market study, those responsible analyzed the range of cleanroom robots offered by the five largest manufacturers, compared them on the basis of a complex requirements profile and made a well-founded decision.
A European development for all types of cleanrooms
The winner of the selection process was the MOTOMAN HD7 from Japanese supplier Yaskawa. This high-performance robot is a new European development for sensitive applications, created in close cooperation with the Fraunhofer Institute for Manufacturing Engineering and Automation IPA. Like its bigger brother, the MOTOMAN HD8, the MOTOMAN HD7 is suitable for use in cleanrooms from class ISO 5 up to the highest GMP class A. It therefore fulfills the requirements that MULTIVAC places on the cleanroom suitability of its robots in every respect.
But the GMP-compliant and cleanroom-compatible design was only one of many aspects that influenced the decision in favor of Yaskawa. Wolfgang Buchenberg comments: “For MULTIVAC, the issue of control technology and integration is also of crucial importance. The Yaskawa ‘MotoLogix’ software interface allows MOTOMAN kinematics, including cobots, to be seamlessly integrated into the MULTIVAC control and software platform, which also ensures centralized line operation from a single source for six-axis robots.
The Yaskawa HD series also features a reduced kinematics design, which offers significant advantages in the pharmaceutical and medical sectors. The routing of cables and connections within the arm, low particle generation and FDA compliance ensure the necessary customer acceptance and facilitate key requirements such as easy cable routing.